
Destylator przemysłowy
Destylator przemysłowy to urządzenie służące do separacji składników cieczy na podstawie różnicy w ich temperaturze wrzenia. Proces ten jest kluczowy w wielu branżach, takich jak chemia, petrochemia czy produkcja alkoholu. Destylacja polega na podgrzewaniu cieczy, co powoduje parowanie substancji o niższej temperaturze wrzenia, a następnie skraplaniu powstałych par. W przemyśle wykorzystuje się różne typy destylatorów, w tym destylatory prostokątne, kolumnowe oraz frakcyjne. Każdy z tych typów ma swoje specyficzne zastosowania i zalety. Na przykład, destylatory kolumnowe są często wykorzystywane w procesach wymagających dużej efektywności separacji, podczas gdy destylatory prostokątne mogą być stosowane do mniej skomplikowanych procesów. Warto również zauważyć, że destylacja może być przeprowadzana w różnych warunkach ciśnienia, co wpływa na wydajność i jakość końcowego produktu.
Jakie są rodzaje destylatorów przemysłowych i ich zastosowania
W przemyśle istnieje wiele rodzajów destylatorów, które różnią się konstrukcją oraz zastosowaniem. Najpopularniejsze z nich to destylatory prostokątne, kolumnowe oraz frakcyjne. Destylatory prostokątne są najprostsze w budowie i najczęściej stosowane do separacji substancji o wyraźnie różniących się temperaturach wrzenia. Ich zaletą jest łatwość obsługi oraz niskie koszty eksploatacji. Z kolei destylatory kolumnowe charakteryzują się bardziej skomplikowaną budową i są wykorzystywane w procesach wymagających wysokiej efektywności separacji, takich jak produkcja alkoholu czy rafinacja ropy naftowej. Destylatory frakcyjne natomiast pozwalają na jednoczesną separację wielu składników cieczy, co czyni je idealnymi do zastosowań w przemyśle chemicznym i farmaceutycznym.
Jakie są kluczowe elementy budowy destylatora przemysłowego
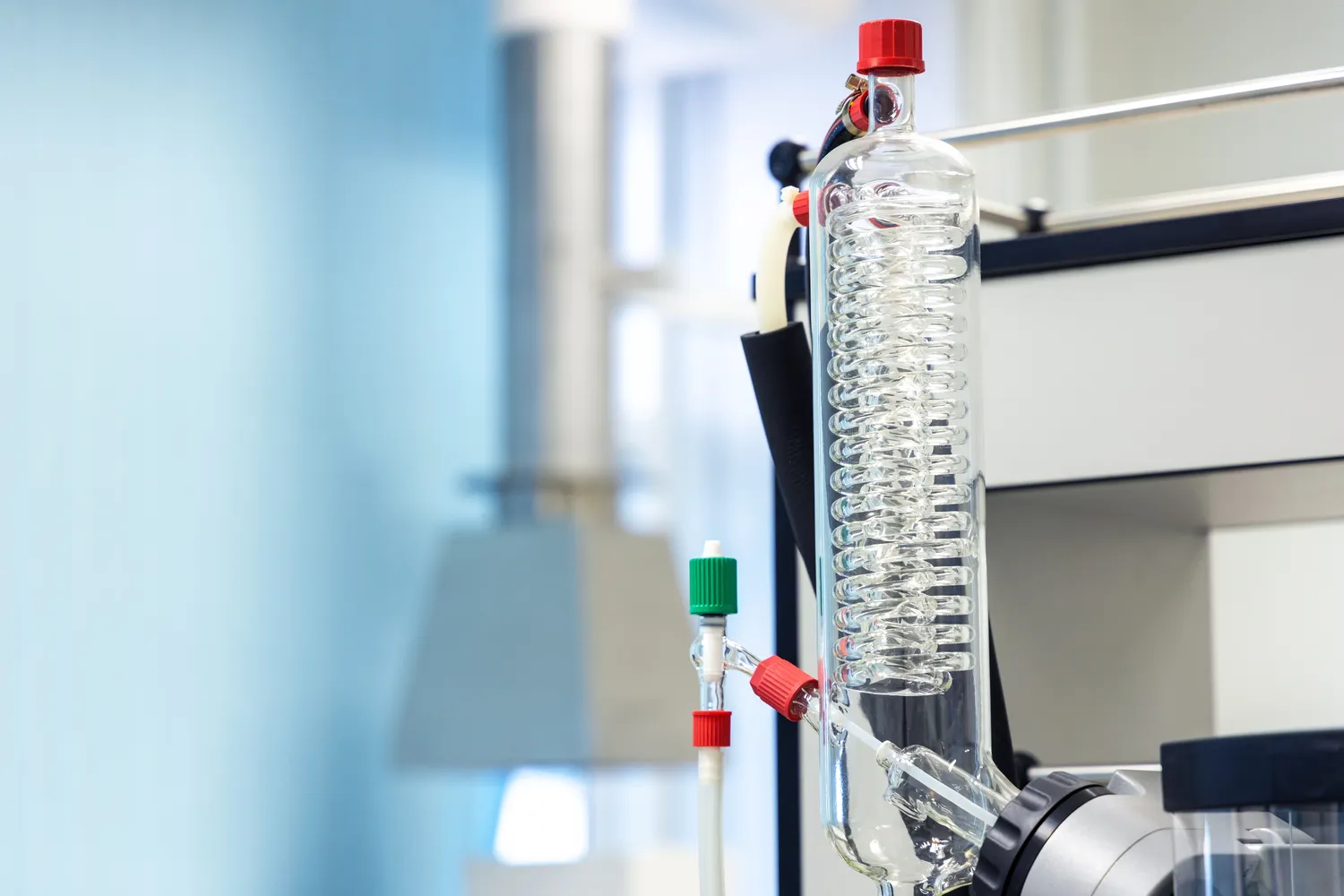
Budowa destylatora przemysłowego opiera się na kilku kluczowych elementach, które mają istotny wpływ na jego wydajność oraz efektywność pracy. Podstawowym elementem jest zbiornik, w którym odbywa się podgrzewanie cieczy. Zbiornik ten musi być wykonany z materiałów odpornych na korozję oraz wysoką temperaturę. Kolejnym ważnym elementem jest system grzewczy, który może być oparty na różnych źródłach energii, takich jak para wodna, olej termalny czy elektryczność. Po podgrzaniu cieczy następuje proces parowania, a powstałe opary przechodzą przez kolumnę destylacyjną lub inny system separacyjny. W przypadku destylatorów kolumnowych istotnym elementem są także tzw. packingi lub talerze, które zwiększają powierzchnię kontaktu między parą a cieczą, co poprawia efektywność procesu. Ostatnim kluczowym elementem jest system chłodzenia, który skrapla pary z powrotem do stanu ciekłego.
Jakie są korzyści z używania nowoczesnych destylatorów przemysłowych
Nowoczesne destylatory przemysłowe oferują szereg korzyści, które przyczyniają się do zwiększenia efektywności procesów produkcyjnych oraz obniżenia kosztów operacyjnych. Przede wszystkim nowoczesne technologie pozwalają na osiągnięcie wyższej wydajności separacji składników cieczy, co przekłada się na lepszą jakość końcowego produktu. Dzięki zastosowaniu zaawansowanych systemów sterowania możliwe jest precyzyjne monitorowanie i regulowanie parametrów pracy destylatora, co pozwala na optymalizację procesów i minimalizację strat surowców. Ponadto nowoczesne urządzenia często charakteryzują się mniejszym zużyciem energii dzięki zastosowaniu innowacyjnych rozwiązań technologicznych, takich jak odzysk ciepła czy automatyczne sterowanie procesami grzewczymi i chłodzącymi. Warto również zwrócić uwagę na aspekty ekologiczne – nowoczesne destylatory są projektowane z myślą o minimalizacji emisji szkodliwych substancji oraz redukcji odpadów produkcyjnych.
Jakie są najczęstsze problemy związane z destylatorami przemysłowymi
Destylatory przemysłowe, mimo swojej zaawansowanej technologii, mogą napotykać różne problemy, które wpływają na ich wydajność i jakość produkcji. Jednym z najczęstszych problemów jest osadzanie się zanieczyszczeń w zbiorniku lub kolumnie destylacyjnej. Zanieczyszczenia te mogą pochodzić z surowców używanych w procesie lub być wynikiem reakcji chemicznych zachodzących podczas destylacji. Osady te mogą prowadzić do zmniejszenia efektywności separacji oraz obniżenia jakości końcowego produktu. Innym problemem jest niewłaściwe ustawienie parametrów pracy, takich jak temperatura czy ciśnienie, co może skutkować nieoptymalnym przebiegiem procesu. W przypadku destylatorów kolumnowych, niewłaściwe rozmieszczenie packingu lub talerzy może również prowadzić do spadku wydajności. Kolejnym istotnym zagrożeniem jest ryzyko przegrzania cieczy, co może prowadzić do powstawania niepożądanych produktów ubocznych.
Jakie są koszty eksploatacji destylatora przemysłowego
Koszty eksploatacji destylatora przemysłowego mogą się znacznie różnić w zależności od wielu czynników, takich jak typ urządzenia, jego wydajność oraz rodzaj przetwarzanych surowców. Podstawowym składnikiem kosztów są wydatki na energię, która jest niezbędna do podgrzewania cieczy i utrzymania odpowiednich warunków pracy. W przypadku dużych instalacji przemysłowych, koszty energii mogą stanowić znaczną część całkowitych wydatków operacyjnych. Kolejnym istotnym elementem są koszty materiałów eksploatacyjnych, takich jak środki czyszczące czy substancje pomocnicze używane w procesie destylacji. Dodatkowo należy uwzględnić koszty związane z konserwacją i naprawami urządzeń, które mogą być niezbędne w przypadku awarii lub zużycia komponentów. Warto również pamiętać o kosztach związanych z przestrzeganiem norm środowiskowych oraz bezpieczeństwa pracy, które mogą wiązać się z koniecznością inwestycji w dodatkowe systemy filtracyjne czy monitorujące emisję substancji szkodliwych.
Jakie są najnowsze trendy w technologii destylacji przemysłowej
W ostatnich latach technologia destylacji przemysłowej przechodzi dynamiczne zmiany, które mają na celu zwiększenie efektywności procesów oraz minimalizację wpływu na środowisko. Jednym z najważniejszych trendów jest rozwój technologii odzysku ciepła, która pozwala na ponowne wykorzystanie energii generowanej podczas procesu destylacji. Dzięki temu przedsiębiorstwa mogą znacznie obniżyć swoje koszty operacyjne oraz zmniejszyć emisję gazów cieplarnianych. Innym istotnym kierunkiem rozwoju jest automatyzacja procesów destylacyjnych. Nowoczesne systemy sterowania umożliwiają precyzyjne monitorowanie parametrów pracy oraz automatyczne dostosowywanie ich do zmieniających się warunków, co przekłada się na wyższą jakość produktów oraz większą stabilność procesów. Również rosnące zainteresowanie ekologicznymi rozwiązaniami sprawia, że coraz więcej producentów inwestuje w technologie minimalizujące odpady oraz emisje szkodliwych substancji.
Jakie są wymagania dotyczące bezpieczeństwa przy użytkowaniu destylatorów przemysłowych
Bezpieczeństwo przy użytkowaniu destylatorów przemysłowych jest kluczowym aspektem, który musi być brany pod uwagę na każdym etapie procesu produkcyjnego. Przede wszystkim należy zapewnić odpowiednie szkolenie dla pracowników obsługujących urządzenia, aby byli świadomi potencjalnych zagrożeń oraz umieli reagować w sytuacjach awaryjnych. Ważnym elementem jest także regularna konserwacja i przegląd techniczny sprzętu, co pozwala na wykrycie ewentualnych usterek zanim staną się one poważnym zagrożeniem. Należy również przestrzegać norm dotyczących ochrony środowiska oraz bezpieczeństwa pracy, co często wiąże się z koniecznością stosowania odpowiednich systemów wentylacyjnych oraz filtracyjnych mających na celu minimalizację emisji szkodliwych substancji do atmosfery. W przypadku substancji łatwopalnych lub toksycznych szczególnie istotne jest zapewnienie odpowiednich środków gaśniczych oraz procedur postępowania w razie wycieku czy pożaru.
Jakie są zastosowania destylatorów przemysłowych w różnych branżach
Destylatory przemysłowe znajdują szerokie zastosowanie w wielu branżach gospodarki, a ich funkcjonalność sprawia, że są niezastąpione w procesach produkcyjnych różnych substancji chemicznych i farmaceutycznych. W przemyśle chemicznym destylacja jest kluczowym procesem wykorzystywanym do oczyszczania surowców oraz separacji produktów ubocznych. Na przykład w produkcji alkoholu stosuje się destylatory do uzyskiwania wysokiej czystości trunków poprzez eliminację niepożądanych składników smakowych i zapachowych. W branży petrochemicznej natomiast destylacja służy do rafinacji ropy naftowej i uzyskiwania różnych frakcji paliwowych, takich jak benzyna czy olej napędowy. Ponadto destylatory są wykorzystywane w przemyśle spożywczym do ekstrakcji olejków eterycznych oraz aromatów z roślin, co ma znaczenie dla produkcji żywności i napojów. W sektorze farmaceutycznym natomiast procesy destylacyjne są stosowane do oczyszczania substancji czynnych oraz produkcji rozpuszczalników wykorzystywanych w formulacjach leków.
Jakie są zalety korzystania z usług profesjonalnych firm zajmujących się dostawą destylatorów
Korzystanie z usług profesjonalnych firm zajmujących się dostawą destylatorów przemysłowych niesie ze sobą wiele korzyści dla przedsiębiorstw planujących inwestycje w tego typu technologie. Przede wszystkim takie firmy dysponują wiedzą i doświadczeniem potrzebnym do zaprojektowania odpowiednich rozwiązań dostosowanych do specyfiki danego zakładu produkcyjnego oraz wymagań dotyczących jakości finalnego produktu. Profesjonalne firmy oferują również kompleksową obsługę serwisową, co pozwala na szybkie reagowanie na ewentualne awarie czy problemy związane z eksploatacją urządzeń. Dodatkowo wiele z nich zapewnia szkolenia dla pracowników obsługujących destylatory, co zwiększa bezpieczeństwo pracy oraz efektywność procesów produkcyjnych. Korzystając z usług renomowanych dostawców, przedsiębiorstwa mogą mieć pewność, że otrzymują sprzęt najwyższej jakości spełniający obowiązujące normy i standardy branżowe.